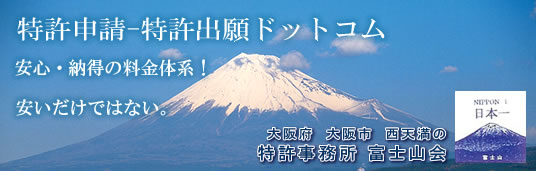
高カロリーガスの製造方法
(書誌+要約+請求の範囲)
(19)【発行国】日本国特許庁(JP)
(12)【公報種別】公開特許公報(A)
(11)【公開番号】特開2000-104080(P2000-104080A)
(43)【公開日】平成12年4月11日(2000.4.11)
(54)【発明の名称】高カロリーガスの製造方法
(51)【国際特許分類第7版】
C10K 3/04
C10L 3/10
【FI】
C10K 3/04
C10L 3/00 K
【審査請求】未請求
【請求項の数】9
【出願形態】OL
【全頁数】7
(21)【出願番号】特願平10-278717
(22)【出願日】平成10年9月30日(1998.9.30)
(71)【出願人】
【識別番号】000000284
【氏名又は名称】大阪瓦斯株式会社
【住所又は居所】大阪府大阪市中央区平野町四丁目1番2号
(72)【発明者】
【氏名】漆崎 靖昌
【住所又は居所】大阪府大阪市東成区中道1丁目4番2号 大阪ガスエンジニアリング株式会社内
(72)【発明者】
【氏名】井上 薫
【住所又は居所】大阪府大阪市東成区中道1丁目4番2号 大阪ガスエンジニアリング株式会社内
(72)【発明者】
【氏名】佐藤 富徳
【住所又は居所】大阪府大阪市中央区平野町四丁目1番2号 大阪瓦斯株式会社内
(72)【発明者】
【氏名】永瀬 真一
【住所又は居所】大阪府大阪市中央区平野町四丁目1番2号 大阪瓦斯株式会社内
(74)【代理人】
【識別番号】100065215
【弁理士】
【氏名又は名称】三枝 英二 (外10名)
【テーマコード(参考)】
4H060
【Fターム(参考)】
4H060 AA01 AA02 BB02 BB12 BB13 BB32 BB34 CC18 DD02 DD04 GG08
(57)【要約】
【課題】高価な炭素源を使用することなく、COGのみを原料として高カロリーガス又は代替天然ガス(SNGともいう。)を低コストで製造できる方法を提供する。
【解決手段】前処理を施した石炭ガスをCO変成し、次いで、膜分離を行って非透過側ガスを採取することを特徴とする高カロリーガスの製造方法、並びに前処理を施した石炭ガスをメタン化反応させ、次いで、膜分離を行って非透過側ガスを採取することを特徴とする高カロリーガスの製造方法。
【特許請求の範囲】
【請求項1】前処理を施した石炭ガスをCO変成し、次いで、膜分離を行って非透過側ガスを採取することを特徴とする高カロリーガスの製造方法。
【請求項2】請求項1の方法によって採取した非透過側ガスを、更に、メタン化反応させることを特徴とする高カロリーガスの製造方法。
【請求項3】前処理を施した石炭ガスをメタン化反応させ、次いで、膜分離を行って非透過側ガスを採取することを特徴とする高カロリーガスの製造方法。
【請求項4】請求項1~3のいずれかの方法によって高カロリーガスを得た後、LPGで増熱することを特徴とする代替天然ガスの製造方法。
【請求項5】13A規格を満たすようにLPGで増熱する請求項4に記載の代替天然ガスの製造方法。
【請求項6】発熱量11000Kcal/Nm3の13A規格を満たすようLPGで増熱する請求項4又は5に記載の代替天然ガスの製造方法。
【請求項7】前処理反応器、CO変成器及び膜分離装置を含む、請求項1の方法で高カロリーガスを製造するために用いる高カロリーガス製造装置。
【請求項8】前処理反応器、CO変成器、膜分離装置及びメタン化反応器を含む、請求項2の方法で高カロリーガスを製造するために用いる高カロリーガス製造装置。
【請求項9】前処理反応器、メタン化反応器及び膜分離装置を含む、請求項3の方法で高カロリーガスを製造するために用いる高カロリーガス製造装置。
詳細な説明
【発明の詳細な説明】
【0001】
【発明の属する技術分野】本発明は、石炭ガス(以下COGともいう。)を原料とする高カロリーガス又はいわゆる代替天然ガス(以下、SNGともいう。)の製造方法、及びその製造方法に用いる製造装置に関する。
【0002】
【従来の技術】近年、都市ガス原料中に占める液化天然ガス(以下、LNGともいう。)の割合は、急激に増加しつつあり、今後ともいわゆる天然ガス転換は更に促進される傾向にある。ところで、LNGは、その運搬、貯蔵、気化等に一定の好適条件下に操業される大規模な設備を要するので、季節、景気変動等に起因する需要変動に必ずしも適切に対応し得ない場合がある。更に、LNGに対する過度の依存は、原料の安定供給の点で若干の問題を生ずる場合もあり得ると考えられる。従って、需要変動の吸収及び原料の多様化により、LNGを主要原料とする天然ガスのメリットを最大限に活用すべく、LNGに依存しないSNGの新しい製造方法の開発が切望されている。
【0003】COGから高カロリーガスを製造する方法としては、例えば、先ずCOGを加圧下でモレキュラーシーブの如き吸収剤の中を通して、吸収剤に吸着される高分子の炭化水素ガスと吸着されない低分子の水素ガスとに分離し、次いで減圧下に炭化水素ガスを吸着剤から脱着させて、高カロリーガスとする方法が考えられる。この場合、吸着装置を複数設けておけば、吸着と脱着とを交互に行なうことにより高カロリーガスを連続的に得ることが可能である。しかしながら、この方法では、吸着剤の機能がCOG中の不純物により阻害され易いため、タール、ベンゾール、ナフタレン等を実質上全量というべき程度まで除去しておく必要があり、大規模な設備が必要となる。
【0004】更にCOGをいわゆるメタネーションにより高カロリーガスに転換させることも考えられるが、この方法においては、COG中の水素が炭素に対して過剰なため、生成ガスの発熱量は所望の値よりもはるかに低いものに留まるという難点がある。
【0005】かかる難点を解決した方法として、特公昭60-8273号に記載された方法がある。この方法は、炭素源としてのナフサ及び/又はLPGを加えた石炭ガスを原料として用い、これを通常の脱酸素、脱硫等の前処理に供した後、ガス化剤及び冷却剤としての水蒸気の存在下にメタン化処理する方法であり、上記の難点を解消するとともに種々の利点を伴ったSNGの製造方法である。具体的には、石炭ガス1モルに対して炭素源としてナフサ及び/又はLPGを0.01~0.1モル加えたCOGを脱酸素、脱硫等の前処理に供した後、入り口温度250~300℃、出口温度300~550℃のメタン化反応器に供給し、S/C=0.5~1.0となる量のガス化剤及び冷却剤としてのスチームの存在下にメタン化することによる石炭ガスを原料とする高カロリーガスの製造方法である。
【0006】しかしながら、この方法では、副原料として高価な炭素源(LPG、ナフサ等)を使用する必要があり、高カロリーガスを得るための製造コストが高くなるという欠点がある。更に、炭素源としてのLPGの使用を不要にすることによって、LPG原料の確保が難しい状況下でもSNGを安定製造する必要性が指摘されている。
【0007】
【発明が解決しようとする課題】本発明の主な目的は、高価な炭素源を使用することなく、COGのみを原料として高カロリーガスあるいは代替天然ガス(SNGともいう。)を低コストで製造できる方法及びその方法に使用し得る製造装置を提供することである。また、本発明の他の目的は、炭素源としてのLPGを不要にすることによって、LPG原料の確保が難しい状況下でもSNGを安定製造できる方法及びその方法に使用し得る製造装置を提供することである。
【0008】
【課題を達成するための手段】本発明者は、上述した如き課題を解決するために鋭意研究を重ねた結果、脱酸素、脱硫等の前処理を施した石炭ガスを原料として用い、これをCO変成した後膜分離する方法、又はメタン化反応させた後膜分離する方法で高カロリーガスを製造することにより、上記目的が達成されることを見出した。
【0009】即ち、本発明は、下記の高カロリーガスの製造方法及び高カロリーガスの製造装置を提供するものである。
【0010】1.前処理を施した石炭ガスをCO変成し、次いで、膜分離を行って非透過側ガスを採取することを特徴とする高カロリーガスの製造方法。
【0011】2.上記項1の方法によって採取した非透過側ガスを、更に、メタン化反応させることを特徴とする高カロリーガスの製造方法。
【0012】3.前処理を施した石炭ガスをメタン化反応させ、次いで、膜分離を行って非透過側ガスを採取することを特徴とする高カロリーガスの製造方法。
【0013】4.上記項1~3のいずれかの方法によって高カロリーガスを得た後、LPGで増熱することを特徴とする代替天然ガスの製造方法。
【0014】5.13A規格を満たすようにLPGで増熱する上記項4に記載の代替天然ガスの製造方法。
【0015】6.発熱量11000Kcal/Nm3の13A規格を満たすようLPGで増熱する上記項4又は5に記載の代替天然ガスの製造方法。
【0016】7.上記項1の方法によって高カロリーガスを製造するために用いる、前処理反応器、CO変成器及び膜分離装置を含む高カロリーガスの製造装置。
【0017】8.上記項2の方法によって高カロリーガスを製造するために用いる、前処理反応器、CO変成器、膜分離装置及びメタン化反応器を含む高カロリーガスの製造装置。
【0018】9.上記項3の方法によって高カロリーガスを製造するために用いる、前処理反応器、メタン化反応器及び膜分離装置を含む高カロリーガスの製造装置。
【0019】
【発明の実施の形態】本発明方法では、原料として石炭ガス(COG)を用いる。本発明方法によれば、LPG、ナフサ等の高価な炭素源を副原料として用いることなく、COGのみを原料として用いるために、高カロリーガス及び代替天然ガス(SNG)を低コストで製造することが可能となる。
【0020】本発明方法で用いるCOGは、前処理を施した後、下記の各処理に供する。前処理としては、脱酸素、脱オレフィン、脱硫等の処理を常法に従って行えばよい。
【0021】例えば、脱硫触媒としての作用を併せ持つ脱酸素反応用触媒である、Ni-Mo系、Co-Mo系等の触媒を用いて前処理を行うことができる。これらの触媒を使用する場合には、原料のCOG中の水素による水添により、COGの脱酸素及び脱有機硫黄が行われる。これらの脱酸素、脱オレフィン、脱硫等の処理は、常法に従って行なえはよく、例えば反応器入口温度200~350℃程度、反応器内圧力5~50kg/cm2G程度、反応器出口温度350~430℃程度の条件下に処理を行なえば良い。また、例えば、COGは吸着脱硫器に送られ、通常のZnOによる吸着脱硫が行われる。
【0022】このようにして、前処理を施されたCOGは、酸素含有量及びオレフィン含有量が実質上零、全硫黄濃度は1ppm以下であることが好ましい。上述の脱硫反応はいずれも発熱反応であるので、必要に応じてCOGから廃熱ボイラー等により熱回収を行なう。
【0023】尚、前処理工程に供給するCOGは、予め、常法に従って、ピッチ、アンモニア、シアン、ナフタリン、ベンゾール等を除去しておく。
【0024】本発明によれば、上述のようにして脱酸素、脱硫等の前処理を施したCOGを用いて、(1)CO変成工程、膜分離工程を経た後、必要に応じて、メタン化工程を経て高カロリーガスを得る方法(第一方法)、(2)メタン化工程、膜分離工程を経て高カロリーガスを得る方法(第二方法)、の二種類の方法によって高カロリーガスを製造することができる。
【0025】尚、これらの方法で得られた高カロリーガスは、このまま使用するできることは言うまでもないが、その後、LPG増熱装置に送給し、LPGを加えて増熱して代替天然ガスとすることもできる。
【0026】以下、上記した二種類の方法について、詳細に説明する。
【0027】(1)第一方法:第一図に示すフローチャートに基づいて、第一方法を説明する。
【0028】前処理反応器(1)において前処理を施されたOCGは、CO変成器(2)に送給されてCO変成処理を施される。CO変成処理としては、鉄-クロム系触媒、銅-亜鉛系触媒等の存在下に、COGに含まれる一酸化炭素ガスを、水蒸気添加により水素ガスと二酸化炭素ガスに変成させる処理を行なえばよい。CO変成器(2)の運転条件は、入口温度200℃~330℃程度の範囲とすればよい。
【0029】その後、CO変成処理を施されたCOGは、膜分離装置(3)に送給される。膜分離装置(3)としては、二酸化炭素を透過し、メタンを透過しないという脱炭酸効率の高い、公知の分離装置を使用ればよい。この様な膜分離装置を用いて膜分離を行うことによって、透過側に炭酸ガスリッチのオフガスが得られ、非透過側に高カロリーガスが得られる。
【0030】さらに、膜分離工程により得られた高カロリーガスは、CO濃度を更に低減して、製品ガスのCO濃度を0.1Vol%未満とするために、メタン化反応器(図示せず)に送給されて、メタン化処理を施される場合も有る。メタン化処理は、白金族金属系触媒、Ni系触媒、貴金属系触媒等の存在下に、S/C(炭化水素中の炭素分子1個当たりの水蒸気中の酸素原子数)が0.0~1.0程度となる量の水蒸気をCOGに加えた状況で行なう。メタン化工程における反応器入口の温度は、230~350℃程度、反応器内圧力は5~10kg/cm2G程度、反応器出口温度は300~550℃程度とするのが好ましい。メタン化反応を終えた生成ガスは、メタン化反応条件により異なるが、COGの当初発熱量が4800~5400Kcal/Nm3であるのに対して、7000~8600Kcal/Nm3程度の発熱量を有する高カロリーガスとなる。
【0031】得られた高カロリーガスは、このまま使用するできることは言うまでもないが、増熱器(4)においてLPGを加えて増熱し、SNG(製品ガスともいう。通常は、発熱量11000Kcal/Nm3の13A規格のSNGである。)とすることができる。
【0032】(2)第二方法:第二図に示すフローチャートに基づいて、第二方法を説明する。
【0033】前処理反応器(1)においてた前処理を施されたCOGは、メタン化反応器(5)に送給され、メタン化処理が施される。メタン化処理は、Ni系触媒、貴金属系触媒等の存在下に、S/C(炭化水素中の炭素分子1個当たりの水蒸気中の酸素原子数)が0.5~1.0程度となる量の水蒸気をCOGに加えた状況で行なうことができる。メタン化工程における反応器入口の温度は250~350℃程度、反応器内圧力は5~10kg/cm2G程度、反応器出口温度は230~550℃程度とするのが好ましい。メタン化反応を終えた生成ガスは、メタン化反応条件により異なるが、COGの当初発熱量が4800~5400Kcal/Nm3であるのに対して、6800~8600Kcal/Nm3程度の発熱量を有する高カロリーガスとなる。
【0034】この生成ガスは、このまま使用するできることは言うまでもないが、更に膜分離装置(3)に送給して、オフガスと高カロリーガスとに分離される。膜分離装置(3)としては、二酸化炭素を透過し、メタンを透過しないという脱炭酸効率の高い分離装置を使用する。この様な膜分離装置を用いて膜分離を行うことによって、透過側にオフガスが得られ、非透過側に高カロリーガスが得られる。
【0035】この様にして得られた高カロリーガスは、このまま使用するできることは言うまでもないが、増熱器(4)において、LPGを加えて増熱し、SNG(製品ガスともいう。通常は、発熱量11000Kcal/Nm3の13A規格のSNGである。)とすることができる。
【0036】
【発明の効果】本発明により、下記の如き顕著な効果が奏功される。
【0037】(1)高価な炭素源を使用することなく、COGのみを原料として高カロリーガスあるいは代替天然ガス(SNGともいう。)を低コストで製造することができる。
【0038】(2)膜分離装置の透過側のオフガスは本発明のプラントの燃料ガス(助燃剤を用いる場合もある。)や製造所の他部署の燃料ガスとして有効に利用されることにより、SNG製造プラントの熱効率を高めることができる。
【0039】(3)本発明方法は、上述の効果に加えて、LPGの導入に伴って、使用量が相対的に低下しているCOGの用途を拡大する点においても極めて有用である。即ち、各種用途を有するコークス製造時の副産物として大量に発生するCOGは、それに対する需要の減少が問題となっていたのであるが、本発明によれば、この問題はCOGのSNGへの転換によって完全に解決される。
【0040】(4)炭素源としてのLPGを不要にすることによって、LPG原料の確保が難しい状況下でもSNGを安定製造できる。
【0041】
【実施例】以下、実施例を示して本発明を更に詳細に説明する。
【0042】実施例1下記表1に示す組成のCOG原料を、Ni-Mo系及び酸化亜鉛系触媒を充填した脱酸素、脱オレフィン、脱硫等を行なう前処理反応器に送給し、反応器入口温度260℃、反応器内圧力8kg/cm2G、反応器出口温度400℃の条件下に前処理した。かくしてCOG中の酸素含有量及びオレフィン含有量は実質上零、全硫黄含有量は1ppm以下となった。
【0043】次いで、前処理を施したCOGを銅-亜鉛系触媒を充填したCO変成器に送給した。CO変成工程は常法に従ってなされ、CO変成器の入口温度は約210℃、出口温度は約260℃、反応器内圧力は約7kg/cm2Gであった。
【0044】CO変成により得られたガスは、更に膜分離装置に送給され、透過側の圧力6.5Kg/cm2G、透過側の圧力0.0Kg/cm2Gの条件下で膜分離を行ない、非透過側にメタンリッチな高カロリーガスを得、透過側に水素リッチなオフガスを得た。
【0045】上記方法で得られた高カロリーガスはそのままで使用することもできるが、LPGで増熱することによって、発熱量11000Kcal/Nm3の13A規格のSNGを製造することができた。
【0046】下記表2に製品ガスを100Nm3/時間とした場合の原料ガス及びオフガスのフローレートを示す。
【0047】このようにして得られた製品ガス(発熱量11000Kcal/Nm3の13A規格のSNG)の組成及び発熱量は、下記表3に示す通りである。
【0048】実施例2下記表1に示す組成のCOG原料をNi-Mo系および酸化亜鉛系触媒を充填した脱酸素、脱オレフィン、脱硫等を行なう前処理反応器に送給し、反応器入口温度260℃、反応器内圧力8kg/cm2G、反応器出口温度400℃の条件下に前処理した。かくしてCOG中の酸素含有量及びオレフィン含有量は実質上零、全硫黄含有量は1ppm以下となった。
【0049】次いで、前処理を施したCOGを白金族系触媒を充填したメタン化反応器に供給し、S/C=0.5となる水蒸気の存在下にメタン化反応を行なった。メタン化反応器の入口温度は約300℃、出口温度は約250℃、反応器内圧力は約7.5kg/cm2Gであった。
【0050】メタン化反応により得られた高カロリーガスは、更に膜分離装置に送給され、透過側の圧力7Kg/cm2G、透過側の圧力0Kg/cm2Gの条件下で膜分離を行ない、非透過側に高カロリーガスを得、透過側にオフガスを得た。
【0051】更に、該高カロリーガスをLPGで増熱することにより発熱量11000Kcal/Nm3の13A規格のSNGを製造することができた。
【0052】下記表2に製品ガスを100Nm3/時間とした場合の原料ガス及びオフガスのフローレートを示す。
【0053】このようにして得られた製品ガス(発熱量11000Kcal/Nm3の13A規格のSNG)の組成及び発熱量は下記表3に示す通りである。
【0054】比較例1下記表1に示す組成のCOG原料と副原料(炭素源)のLPGを混合し、この混合ガスをNi-Mo系及び酸化亜鉛系触媒を充填した脱酸素、脱オレフィン、脱硫等を行なう前処理反応器に送給し、反応器入口温度300℃、反応器内圧力7.5kg/cm2G、反応器出口温度250℃の条件下に処理した。かくしてCOG中の酸素含有量及びオレフィン含有量は実質上零、全硫黄含有量は1ppm以下となった。
【0055】次いで、前処理を行なった混合ガスを、貴金属系触媒を充填したメタン化反応器に供給し、S/C=0.8となる水蒸気の存在下にメタン化反応を行なった。メタン化反応器の入口温度は約300℃、出口温度は約250℃、反応器内圧力は約7.5kg/cm2Gであった。
【0056】次いで、メタン化反応工程によって得られた高カロリーガスをLPGで増熱することにより発熱量11000Kcal/Nm3の13A規格のSNGを製造することができた。
【0057】下記表2に製品ガスを100Nm3/時間とした場合の原料ガス及び副原料ガスのフローレートを示す。
【0058】このようにして得られた製品ガス(発熱量11000Kcal/Nm3の13A規格のSNG)の組成及び発熱量は、下記第3表に示す通りである。
【0059】
【表1】
【0060】
【表2】
【0061】
【表3】
【0062】以上の結果から明らかなように、本発明方法によれば、COGのみを原料として、安価に発熱量11000Kcal/Nm3の13A規格のSNGを製造することができた。